In mechanical automation movement, the motor is an indispensable component. In the classification of motors, the most common and important motors are DC gear motors and stepper motors. Although they are both motors, there are great differences between the two. The following will introduce the difference between DC reduction motors and stepper motors in detail.
DC reduction motor
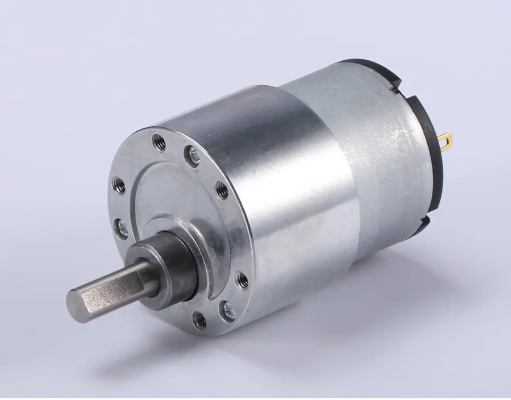
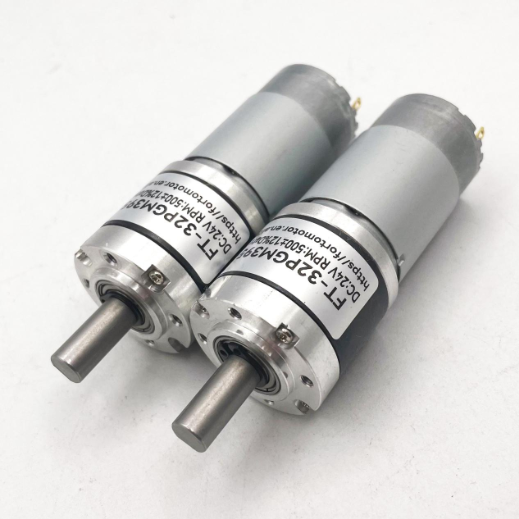
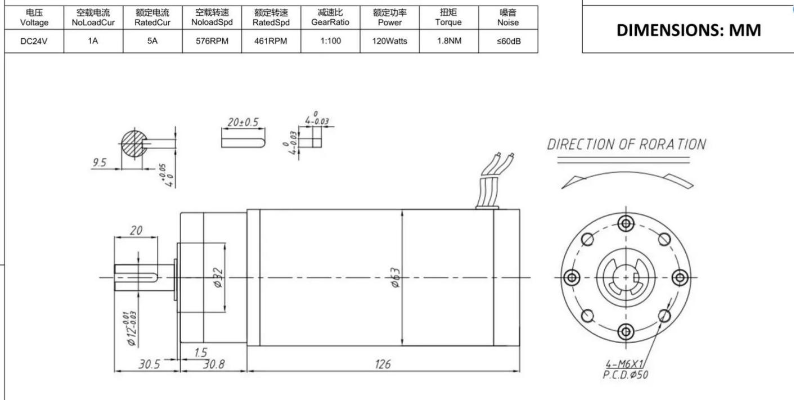
1. Working principle
The DC gear motor changes the polarity of the magnetic field inside the motor by the positive and negative current of the external current, thereby realizing the rotation of the motor. The output shaft of the DC geared motor is integrated with a reducer to reduce the output rotation speed and increase the torque of the motor to ensure that the motor can adapt to the load.
2. Features
The DC gear motor has high efficiency, a wide working range, and low monetary value. It is particularly suitable for application scenarios requiring high torque, such as mechanical loads and automatic control systems, but at the same time, due to its large electromagnetic loss, maintenance and troubleshooting require certain professional skills.
Stepper motor
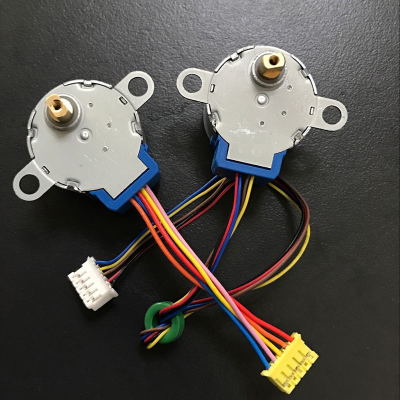
Working principle 1.
A stepper motor drives the motor to rotate at a certain angle by continuously changing the polarity of its electromagnetic field when powered on. It is divided into two types: one is a single-phase stepper motor and the other is a three-phase stepper motor. The output shaft of the stepper motor is combined with a converter or a reducer to control the angle and speed.
Features
Stepper motors have high precision, precise control, and can restart and start automatically. They are particularly suitable for application scenarios with high-precision control requirements, such as digital printers, laser scanners, and LCD displays. However, at the same time, since the stepper motor drive shaft has mechanical noise, stepper motors are not the best choice when low-noise operation is required.
The difference between DC reduction motor and stepper motor
Differences | DC gear motor | Stepper motor |
Working principle | Change the polarity of the magnetic field inside the motor by applying positive and negative current
|
By continuously changing the polarity of its electromagnetic field when powered on, the motor is driven to produce a certain rotation angle |
Output shaft | Integrated reducer to reduce the output rotation speed and increase the torque of the motor | Combined with a converter or reducer, it can control the angle and speed |
Application scenarios | Suitable for scenarios requiring high torque such as mechanical loads and automatic control systems | Suitable for high-precision control and restart self-starting application scenarios, such as digital printers, laser scanners, LCD displays |
Advantages | High efficiency, wide working range, low monetary value | High precision, precise control, and continuous restart self-starting |
Disadvantages | High electromagnetic wear, requiring professional skills for maintenance and troubleshooting | The drive shaft has mechanical noise |
Conclusion
In short, DC gear motors and stepper motors have their own advantages and disadvantages, and their application scenarios are also different. For some scenarios that require high flexibility control and high precision, such as welding robots and CNC, stepper motor control is generally used, while scenarios that require fast, efficient, reliable, and not very high precision requirements, such as assembly line conveyors, are generally controlled by DC reduction motors.
Post time: Oct-18-2024