As the name implies, micro gear reduction motors are composed of gear reduction boxes and low-power motors. They are widely used. FORTO MOTOR micro gear reduction motors can be used in kitchen appliances, medical equipment, security equipment, experimental equipment, office equipment, power tools, etc. Of course, there are many types of micro gear reduction motors, and manufacturers should choose motors according to their needs.
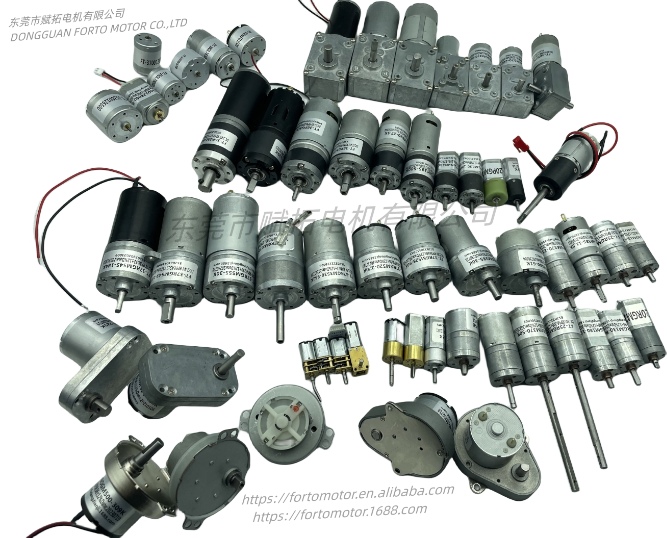
The following are the matters on how to select micro gear reduction motors:
1. Determine the basic parameters
The basic parameters of the motor include: rated voltage, rated speed, rated torque, rated power, torque and gearbox reduction ratio.
2. Motor working environment
Is the motor working for a long time or a short time? Wet, open-air occasions (corrosion protection, waterproof, insulation grade, protective cover when M4), and the ambient temperature of the motor.
3. Installation method
The motor installation methods include: horizontal installation and vertical installation. Is the shaft selected as a solid shaft or a hollow shaft? If it is a solid shaft installation, are there axial forces and radial forces? The structure of the external transmission, the flange structure.
4. Structural scheme
Is there any non-standard requirement for the direction of the outlet shaft, the angle of the terminal box, the position of the outlet nozzle, etc.
The main feature of the micro gear reduction motor is that it has a self-locking function. Its advantages are compact structure, high precision, small return gap, small size, large transmission torque and long service life. The motor is designed and manufactured on the basis of the module combination system. There are many motor combinations and installation methods, structural schemes, and the transmission ratio is finely graded to meet different working conditions and realize mechatronics.
The main feature of the micro gear reduction motor is that it has a self-locking function. Its advantages are compact structure, high precision, small return gap, small size, large transmission torque and long service life. The motor is designed and manufactured on the basis of the module combination system. There are many motor combinations and installation methods, structural schemes, and the transmission ratio is finely graded to meet different working conditions and realize mechatronics.
In the micro DC reduction motor, the reduction box is of various types, and the shaft output method is also designed according to different needs. Common ones are center output shaft, reverse output shaft and side output shaft (90°), and there is also a double output shaft design. The gear stage of the center output reduction motor is relatively small, so its precision is higher than other output methods, and the noise and weight are relatively small, but the load capacity will be relatively low (compared to the reduction motor, of course the center output method is sufficient), while the load capacity of the reverse output micro DC reduction motor will be larger, because it has more gear stages, but the precision is lower and the noise will be slightly louder.
Generally, the micro DC reduction motor uses the N series, such as N10\N20\N30, etc. (all models can be used as reduction motors, and the reduction box can be added). The voltage is mostly controlled within 12V for the best. Too high voltage will make the micro DC reduction motor noisier and shorten its life.
At present, most of the reduction motors on the market use 12 reduction gearboxes, and micro motors use N20 ordinary brushes (the service life of carbon brushes will be slightly longer), which can be equipped with photoelectric encoders or ordinary encoders. Photoelectric encoders for N20 motors are mostly used in high-precision products. The encoder will feedback 48 signals when the micro DC motor rotates one circle. Assuming the reduction ratio is 50, the output shaft of the reducer will receive 2400 signals when it rotates one circle. Only some equipment that requires ultra-high precision control will use it.
The carbon brush material and bearings of the micro DC reduction motor will affect the life. When choosing a reduction motor, if the ordinary brushed DC motor cannot meet the life requirements and you don’t want to change the brushed motor, you can replace the ordinary brush with a carbon brush, replace the oil-bearing bearing with a ball bearing, or increase the gear modulus to increase the service life of the micro DC motor.
There is usually a misunderstanding in the selection of micro DC reduction motors. The smaller the size, the better, the greater the torque, the better, and some even require silence. This not only increases the selection time of the micro motor, but also increases the cost. For the mechanical size of the micro DC motor, it is only necessary to select it according to the maximum installation space that the product can accept (not a fixed size, otherwise it is necessary to open the mold, which increases the cost). For the output torque, just choose the appropriate one. The greater the torque, the more gear stages, and the cost will be greatly increased. As for the requirement of silent micro DC reduction motors, it is currently difficult to achieve. The only way is to improve the noise. The causes of noise include current noise, friction noise, etc. For micro DC reduction motors, these noises can be ignored.
Post time: Oct-16-2024