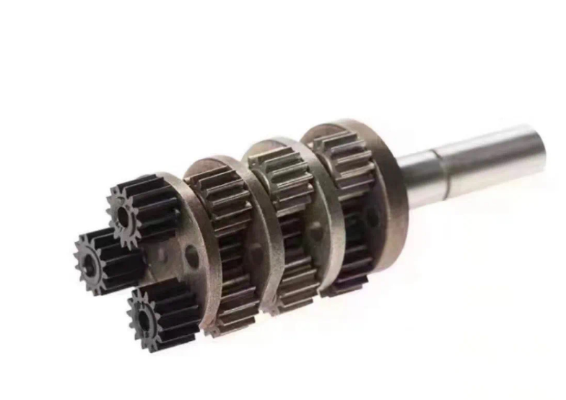
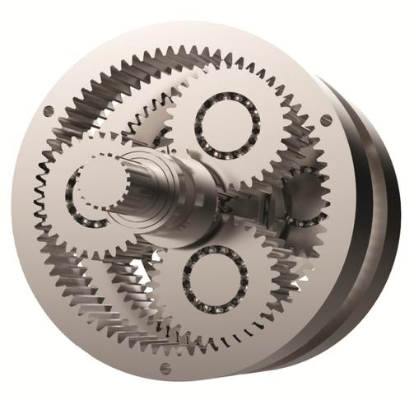
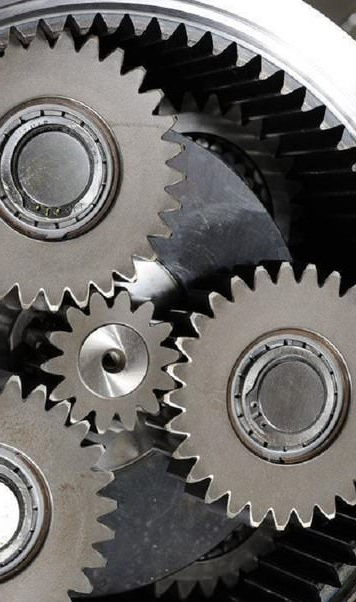
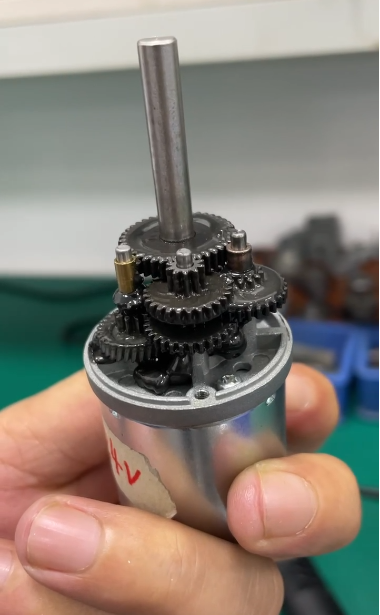
The core working principle of the micro reduction gear motor is to reduce the speed and increase the torque through gear transmission. Micro reduction motors use the transmission of gear pairs at all levels to achieve the purpose of speed reduction. For example, a small gear driving a large gear can achieve a certain reduction effect. Through a multi-stage structure, the speed can be greatly reduced. This working principle allows micro reduction motors to play an important role in applications requiring low speed and high torque.
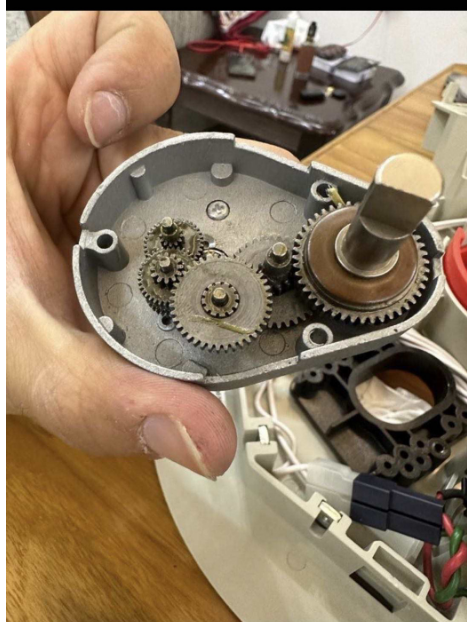
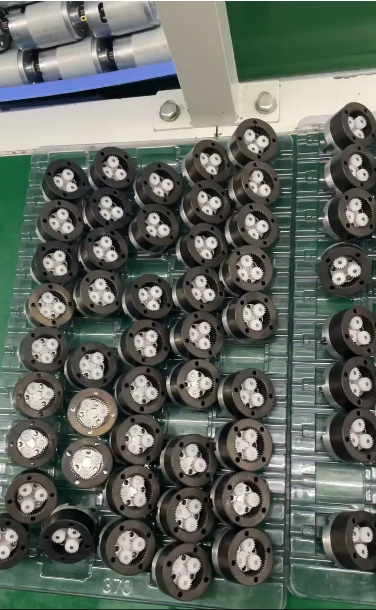
The application of gears in micro gear motors is mainly reflected in their structure and function. Micro gear reduction motor is a micro motor-driven closed transmission reduction device, which is usually assembled and supplied by a professional reduction motor manufacturer. This combination can not only reduce the speed and increase the torque, but also has the characteristics of low energy consumption, superior performance, small vibration and low noise. The structural principle of the gear reducer includes the combination of sun gear and planetary gear, which achieves a higher reduction ratio through multi-stage gear transmission to meet the working needs of various mechanical equipment
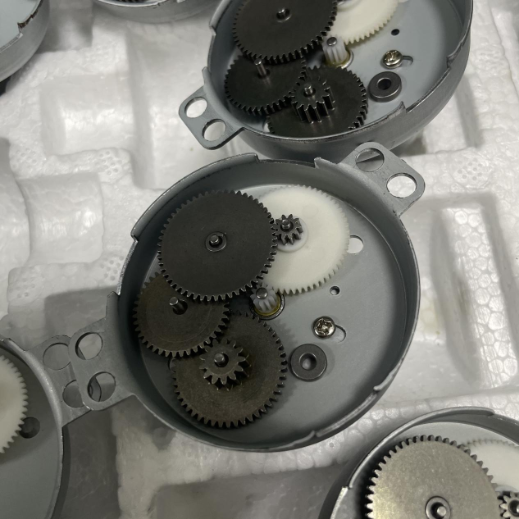
The application fields of micro reduction motors are very wide. Mainly used in small light industrial machinery, automation equipment, home appliances and other fields. For example, in light industrial machinery in the packaging, food, textile and cosmetics industries, micro-geared motors can improve work efficiency. In automation equipment, especially production lines, micro gear motors play an important role by adjusting their speed according to user needs. In addition, in home appliance applications such as soymilk machines, juicers, refrigerators, and washing machines, micro reduction motors provide stable performance and operation
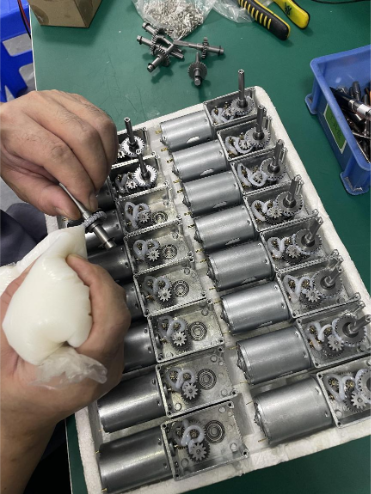
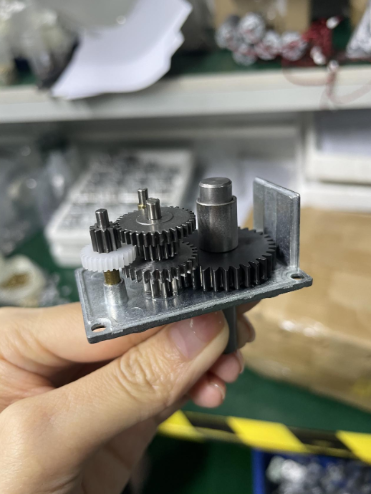
Making and measuring in micro MIM manufacturing
A gearwheel is a component within a transmission device that transmits rotational force to another gear or device and is also a machine element for high accuracy positioning. In recent years some advanced micro-manufacturing processes and micro-sized gears made of metals and some advanced ceramics have been manufactured [1]. Micro-planetary gear motors have also been made from nickel-ferrous (Ni-Fe) and nickel-based bulk metallic glasses by X-ray lithography & electro-deposition (direct-LIG) [2] and injection molding [3], respectively. /
However, there is demand for micronized gears made of general-purpose durable materials for miniaturization and reliability improvement of various products. In manufacturing terms the aim is to achieve a high economic efficiency to satisfy industrial need. Micro metal powder injection molding (μ MIM) is useful for producing micro-sized and microstructured parts [4-5], but measuring the accuracy of micro-gears manufactured by μ MIM has proved difficult. /
A micro-planetary gear made of 17-4PH stainless steel was manufactured by μ MIM as part of the Osaka project. The quality of the ultra-compact planet gear was evaluated by measuring the variation in dimensions of the gear teeth with digital image analysis. The micro-planetary gear composed of three types of gearwheels manufactured by μ MIM process is shown in Figure1. In this study, the accuracy of the planet gear with dimensions shown in Figure 1(c) was evaluated. The specification of the planet gear (as sintered) is shown in Table 1. /
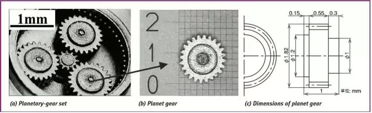
Figure 1. Micro-planetary-gear manufactured by μ MIM. (a). Planetary-gear set; (b) . Planet gear; (c). Dimensions of planet gear /
Table 1. Specification of planet gear (as sintered).The materials used for producing the ultra-compact gears were stainless steel 17-4PH water-atomized powder (D50=2μm) and poly-acetyl based binders. Powder loading of the feedstock was 60vol%. The feedstock was injection-molded using a high-speed injection molding machine (FANUC Ltd., S-2000i 50A). The green compacts were de-bound at 600ºC for two hours in a nitrogen atmosphere, and sintered at 1150ºC for two hours under argon. The sintered parts were also age-hardened at 480ºC for one hour. /
The accuracy of conventional-sized gears is generally evaluated by master gear meshing test or contact profilometry. However, in the case of compact gears it is difficult to manufacture the master gear and to measure the shape by contact. Therefore a noncontact shape measurement technique using advanced instruments such as laser displacement sensing and digital image analysis are considered useful in evaluating the accuracy of ultracompact gears. /
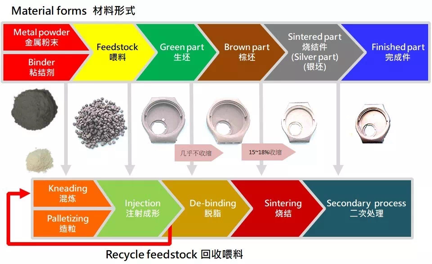
Post time: Oct-14-2024